|
|

REMOVING THE JAGUAR ENGINE |
Making the First Cut

I hadn't quite internalized the fact that the Jaguar's hood opens from the rear, which
would make it really hard to work on the front of the engine bay. So I went on the
internet and found that it was pretty simple to pull the hood. You disconnect the gas
struts, remove the front grille, then reach through the open grille and unbolt the four
hood bolts. Be sure to mark the location of the hood on the hinges with a marker or an
awl. Then you and your assistant (Linda) lift the hood off and prop it against the wall
with suitable padding. |
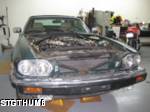
|
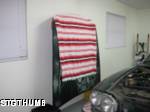 |
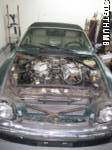 |
That was easy. Next it was clear that the plastic piece behind the front air dam had to
come off. That took a few bolts, and I had access to the underside of the radiator.
That was enough for one day. |
Some Serious Wrenching
I didn't have a service manual yet, but it was pretty clear that the radiator and A/C
condensor had to come out. I removed the lower radiator hose and drained the radiator into a five gallon bucket. Then I removed the radiator header plate. I removed the
bizarro soldered brass tubing apparatus on top of the radiator header plate. Before I
could remove the header plate I had a policy decision to make. There were two fuel
injection-looking connectors on top of the plate, each connected to what looked like an
aluminum heatsink, but which had to be more complex. The heatsinks both said Marelli
on them, and were cast, so I figure they were either injection- or ignition-related.
There was no way to get the connectors free of the header plate because the wiring
passed through a small hole in the plate -- the connectors must have been attached in
place. On the spot I adopted a policy of destruction when required, and cut the wiring
so I could remove the connectors, and then
the header plate itself. Next was the rest of the radiator hoses, the transmission
cooler lines, and then the radiator.
The previous owner had said that the A/C was not working, so I removed the lines to the
condensor, without a cloud of freon. I removed the condensor, and what I'm guessing
is a muffler/dampener on the front of the condensor. That was enough work for one day.
I cleaned up the car, mopped up the spilled coolant and ATF, and turned off the lights.
|
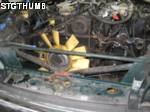 |
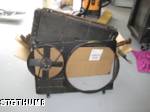 |
 |
|
References Required
I realized I needed some sort of service manual. I could probably gnaw away at the
wiring, mounts, and various lines, until the engine was ready to come out, but it would
be a lot easier with some directions. I looked on line, but couldn't find a Haynes or
a Chilton's manual. I did find a couple copies of the factory service manual for about
$400. Finally I found some CD versions of the manual on eBay. Normally I really dislike
CD manuals, but they do have their uses. For one thing, you can print out pages you
need for a procedure, and not worry about getting them dirty. The drawbacks are that you
can't flip through the manual to quickly find what you want, and you can't use the
computer without getting it dirty. Maybe I need a cheap old PC, and a waterproof
membrane keyboard. Throughout this project I will be resisting the urge to get
sidetracked with things like setting up a PC to read the CD manual. That's why I have
no plans to upgrade the LT1. I think I could easily spend a lot of time and money
doing a full or partial rebuild on the engine. But it is already running! I want the
straightest path to get to a running Jaguar. I did take the time to prepare the
garage, but I think that will pay off in a big way by giving me a comfortable place to
work, which means I will be more likely to stick with the project. Anyway, I bought
the CD manual off eBay, and will be awaiting its arrival. Until then I will have to
find some simple things to do on the car.
Tonight I removed and/or loosened most of the clamps on the exhaust, just for
something to do.
When I got home tonight the Jaguar service manual on CD was
waiting for me in the mailbox. Now I can read it to find out how to remove
the engine.
Expert Advice
This morning
I talked with Andrew from Jaguar
Specialties today, and he basically walked me through the entire engine
removal process. It didn't have much in common with the version in the CD
manual. I wrote it all down, and got started. The details are
here if you are
interested. I was able to remove
the exhaust, the injection wiring harness, and the other wires and hoses.
All I have left is the driveshaft, transmission mount, and engine mounts.
Then find an engine lift, and pull the engine. |
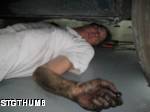 |
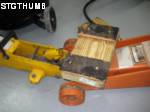 |
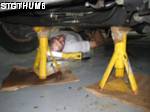 |
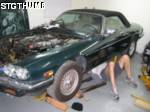 |
I've been making more incremental progress. The engine wiring harness is
completely removed from the engine. I've cut the fuel lines and power
steering lines. And a lot of the heat shields and panels around the
transmission and driveshaft are out. There's still more things to remove
I have an engine hoist now. I tried to borrow one, and to find one on
craigslist, but didn't have any success. Part of the reason I didn't want
to buy one is that I'll have to store or dispose of it when this project
is over.
Of course, I might fall in love with engine swaps and use it regularly.
Anyway, I bit the bullet and went into Harbor Freight, and found that the
2 ton folding lift I wanted was on sale from $219 marked down to $149.
Add in the 20% coupon I had, and I was out the door with a 2 ton lift and
4 ton load leveller for $168. I've got the lift assembled, and it looks
like it should do the job fine.
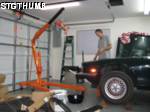
Things have been going pretty well. There have been some fasteners in
awkward
places, but nothing rusted or stripped, and no snapped bolts or studs. There
is a coating of oil and other fluids that seems to have kept everything well
lubricated. A few bolts have been surprisingly loose. The exhaust manifold
stud nuts, and the driveshaft nuts were hand-tight.
The rest of the engine wiring is off. I finally just kept going after every
connector and wire until there was nothing connected to the engine. I got
the
ground strap off the engine, and removed the starter power cable at the
firewall.
I removed the brace across the front of the engine compartment. I'm not sure
it's absolutely necessary, but it will give a few more inches of clearance
when
removing the engine.
The engine is out!
I was out in the garage last night removing the
transmission
mount, which is by far the most complex I have ever seen. It has three
plates
and a big coil spring that seems to suspend the tail of the transmission. I
got everything out except the last plate, which would not come loose. Andrew
had told me that there were a couple ears on one of the plates, which extend
up into the tunnel and are hard to see, but I couldn't spot them. After ten
minutes of looking I finally found them, and got the plate out. After that I
had the driveshaft off in another ten minutes. I removed the shifter and the
speedometer pickup, and I was done!
![]()
Tools
A brief digression about tools. I have basic hand tools I have acquired over
the years, mostly Craftsman and Husky, but more recently I have bought a few
used Snap-On items off the internet. So far in this project I have not been
stuck for lack of a tool. This whole car has come apart with:
- Small Craftsman 1/4" ratchet set. A long extension and a medium
extension
were invaluable, as was a universal joint.
- Small Husky 3/8" ratchet set. My aunt gave this to me years ago, and I
have used it constantly. I also have a set of super-cheap deepwell sockets I
bought when I was in school, that I have not yet been able to destroy. I
have a
simple Craftsman breaker bar, and a piece of gas pipe to go with it.
And I recently bought a used Snap-On ratchet on eBay. I don't think it works
any better than the Husky ratchet, but it is nice to know I'm using a
Snap-On.
- I have a basic 1/2" set that never fails on the big nuts.
- I have a complete set of Husky combination wrenches that are nice, with a
small box end that fits in most places, that was a gift from my dad.
- He also gave me a set of GearWrenches, which are ratcheting combination
wrenches. I use these when possible, bu the set is not as complete as the
Husky set, so sometimes I have to use a non-ratcheting wrench. The only
tools
I have contemplated buying are more GearWrenches to fill in the gaps in the
set.
- I have an assortment of Craftsman screwdrivers, and a couple Snap-Ons
that
came from eBay.
- I have a bunch of (mostly) crappy pliers. I primarily use a big pair of
ChannelLock knockoffs, some wire cutters, and a pair of real ViseGrips.
That's about all of the tools that I have used on the car. I did have to dig
up a PoziDrive #3 bit for a couple screws, and I used a hacksaw to cut some
hoses, but those are the only exceptions.
Anyway, the engine is out. It went pretty simply. I had the rear of the car
raised, as Andrew suggested. The transmission pan was supported by a small
jack after I had removed the cross brace. Then I hooked up the hoist and the
load leveller. I had paid an extra $5 for the 4 ton leveller instead of
the 2
ton, thinking that the larger one would work more smoothly. I think it did.
I began jacking up the engine hoist, and checking for obstructions or
hangups.
I lowered the jack under the transmission, and used the leveller to raise the
front of the engine and lower the rear. The four lifting ears on the engine
made it really easy to hook up. I found one quote on the internet that said
Don't know about a 96, but back in the 70s, they used to say that they put
those
engine lift tabs on them at the factory, so you could hook a chain on it and
yank it to put a SB Chevy in there.
|
|
|
|